L’évolution du procédé de traitement thermique de Safran Landing Systems
En 2007, Safran Landing Systems modernise un de ses procédés de traitement thermique pour ses pièces avionnables. Jusqu’alors, l’entreprise procédait à un traitement en bain de sel.
Cette méthode, bien qu’efficace, dégage des vapeurs et fumées toxiques et peut s’avérer dangereuse pour les salariés. Safran a alors décidé, après plusieurs années de réflexion et d’ingénierie, d’automatiser entièrement ce procédé en utilisant des fours de traitement technique.
Elle conserve les mêmes outillages pour la préhension et le support des pièces avionnables.
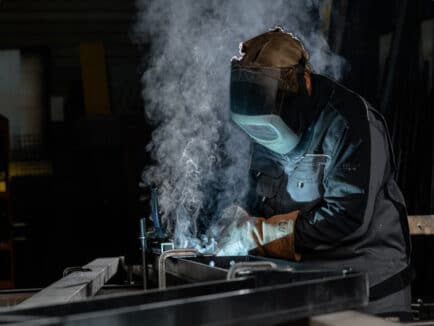
Un outillage complexe pour répondre à des contraintes de température et de poids.
Mais alors que ces outillages étaient adaptés au traitement en bain de sel, l’entreprise constate que dans les fours les outils se dégradent beaucoup plus et ne sont pas prévus pour soutenir des pièces aussi conséquentes (environ 3 mètres de diamètre par 5 mètres de hauteur) à des températures aussi élevées.
La naissance du portique TTH, un défi relevé par OACA.
Safran Landing Systems fait appel à son réseau de sous-traitants pour trouver une solution.
C’est le groupe OACA qui est retenu après une proposition commerciale et technique pour les outillages porteurs : les portiques TTH.
Le bureau d’étude doit concevoir une pièce avec un cahier des charges complexe et prendre en compte le phénomène de fluage : avec la chaleur, la matière se déforme et finit par ne plus être fonctionnelle.
Le bureau d’étude conseille Safran sur la conception des outillages pour qu’ils résistent le mieux possible à ce phénomène de fluage et optimise la conception pour simplifier la fabrication tout en conservant la résistance.
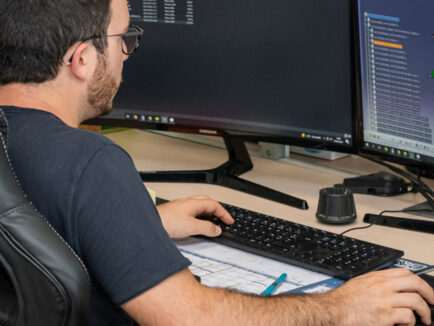
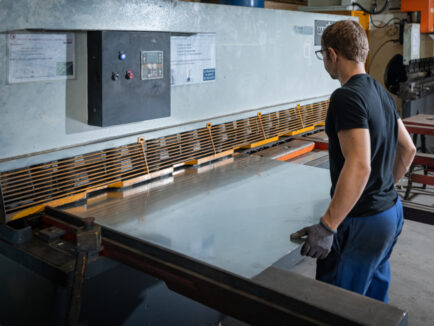
La fabrication, le contrôle
et la livraison : la qualité
de bout en bout.
OACA Métallerie et OACA Usinage travaillent alors main dans la main et font appel à des partenaires de confiance pour relever
le défi de créer ces pièces hors-normes pouvant résister à 120 passages en rouge incandescent et en organisent la fabrication et la livraison de façon récurrente.
L’embase est réalisée chez OACA Métallerie avec une cintreuse à galet, des plaques découpées avec une découpe laser et des procédés de soudage.
OACA Usinage réalise le bras central d’une épaisseur de 50mm sur 1600mm de longueur. Ce bras est particulièrement important: c’est lui qui doit être en capacité de résister à une charge supérieure à 2 tonnes.
OACA Usinage réalise également les autres pièces pour le levage, la sécurisation, et la préhension au crochet sur ses centres d’usinage Haas.
Découvrez le déroulement du projet
et les solutions proposées
par OACA.
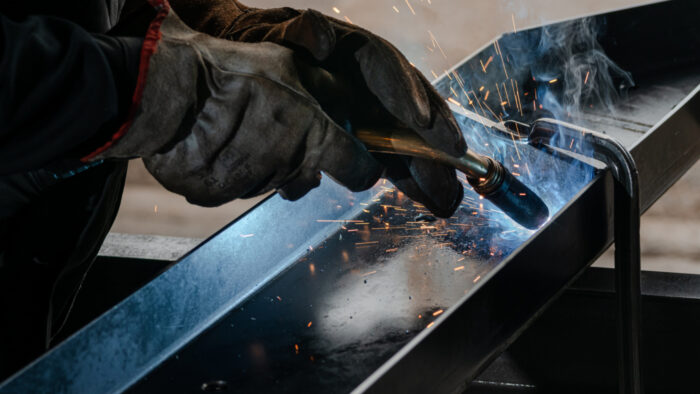
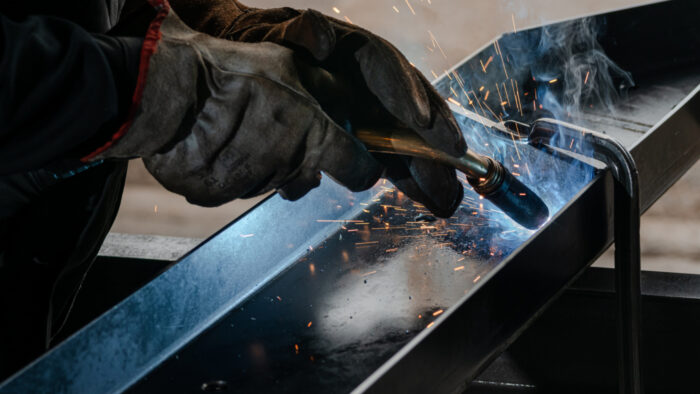
OACA améliore sa production
afin de minimiser les coûts
pour Safran.
Au fil des années, la fabrication évolue et OACA simplifie la géométrie des pièces et donc la fabrication pour apporter un meilleur soutien, un gain en longévité et l’optimisation des coûts pour Safran Landing Systems.
L’ensemble est ensuite contrôlé sur deux aspects.
D’abord, la géométrie du portique. Ensuite, la capacité en charge. Un essai en charge est réalisé pour s’assurer que la pièce résistera bien à la charge maximale de 2025 kg accrochée
à l’anneau supérieur.
Le portique conforme est ensuite basculé à l’horizontale pour être transporté à l’aide d’un outillage de transport spécifiquement conçu pour lui. Il est chargé sur camion à l’aide d’un chariot élévateur et livré directement chez Safran Landing Systems.
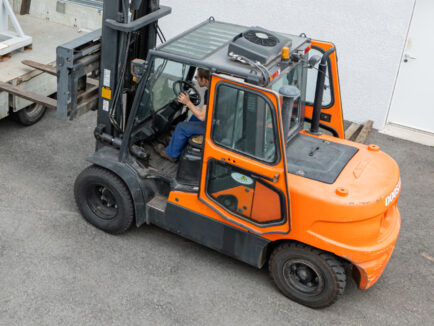